What is Duplex Stainless Steel? An Introduction to Its Family and Basic Properties
Duplex stainless steel (DSS) is a unique class of stainless steel characterized by a dual-phase microstructure, blending approximately equal proportions of austenite and ferrite. This hybrid structure distinguishes it from traditional stainless steels, which are predominantly austenitic (e.g., 304, 316) or ferritic (e.g., 430).
Developed initially in the 1930s but significantly refined since the 1970s, duplex stainless steels have evolved into a diverse family of alloys that address specific industrial challenges. With global demand increasing at approximately 5-7% annually, these materials have moved from niche applications to mainstream industrial use in just a few decades.
The Major Grades of DSS family
The DSS family contains several key grades, each optimized for specific environmental challenges.
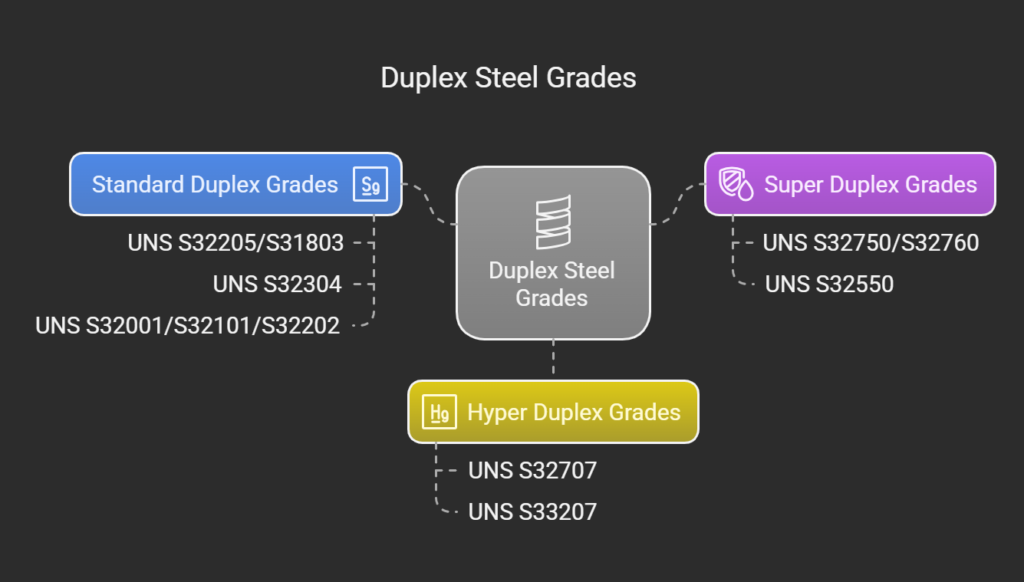
Standard Duplex Grades
- UNS S32205/S31803 (2205): The most widely used duplex grade, accounting for over 80% of duplex applications. f
- UNS S32304 (2304): A lean duplex grade with lower nickel and molybdenum content.
- UNS S32001/S32101/S32202: Newer lean duplex grades designed for cost-efficiency.
Super Duplex Grades
- UNS S32750/S32760 (2507): Higher alloyed for extreme corrosion resistance.
- UNS S32550/S32550: Variants with additional elements for specialized applications.
Hyper Duplex Grades
- UNS S32707/S33207: The most highly alloyed duplex grades for the most demanding environments.
The DSS family’s grades—each tailored to specific applications. Its basic properties include high tensile strength (often twice that of austenitic stainless steel), excellent resistance to Stress Corrosion Cracking (SCC), and superior durability in aggressive environments. These attributes stem from its balanced microstructure, making DSS a versatile solution for industries like oil and gas, chemical processing, and construction.
Chemical Composition and Physical Properties
The exceptional performance of duplex stainless steels stems from their carefully balanced chemical composition. While specific formulations vary between grades, all duplex stainless steels share certain key elements:
Composition by weight (%)
Grade | UNS equiv | C, max. | Si | Mn | P, max. | S, max. | N | Cr | Cu | Mo | Ni | Other |
Standard Duplex | S32202 | 0.03 | ≤1.00 | ≤2.00 | 0.04 | 0.010 | 0.16 to 0.28 | 21.5 to 24.0 | – | ≤0.45 | 1.00 to 2.90 | – |
Standard Duplex (Lean) | S32304 | 0.03 | ≤1.00 | ≤2.00 | 0.035 | 0.015 | 0.05 to 0.20 | 22.0 to 24.5 | 0.10 to 0.60 | 0.10 to 0.60 | 3.5 to 5.5 | – |
Standard Duplex (Lean) | S32101 | 0.04 | ≤1.00 | 4.0 to 6.0 | 0.040 | 0.015 | 0.20 to 0.25 | 21.0 to 22.0 | 0.10 to 0.80 | 0.10 to 0.80 | 1.35 to 1.90 | – |
Standard Duplex | S31803, | 0.03 | ≤1.00 | ≤2.00 | 0.035 | 0.015 | 0.10 to 0.22 | 21.0 to 23.0 | – | 2.50 to 3.50 | 4.5 to 6.5 | – |
Standard Duplex | S32205 | 0.03 | ≤0.70 | 2.5 to 4.0 | 0.035 | 0.005 | 0.20 to 0.30 | 23.0 to 25.0 | 0.10 to 0.80 | 1.00 to 2.00 | 3.0 to 4.5 | |
Super Duplex | S32520 | 0.03 | ≤0.70 | ≤2.00 | 0.035 | 0.015 | 0.20 to 0.30 | 24.0 to 26.0 | 1.00 to 2.50 | 3.0 to 4.0 | 6.0 to 8.0 | – |
Super Duplex | S32750 | 0.03 | ≤1.00 | ≤2.00 | 0.035 | 0.015 | 0.24 to 0.35 | 24.0 to 26.0 | – | 3.0 to 4.5 | 6.0 to 8.0 | – |
Super Duplex | S32760 | 0.03 | ≤1.00 | ≤1.00 | 0.035 | 0.015 | 0.20 to 0.30 | 24.0 to 26.0 | 0.50 to 1.00 | 3.0 to 4.0 | 6.0 to 8.0 | W 0.50 to 1.00 |
Hyper Duplex | S32906 | 0.03 | ≤0.50 | 0.80 to 1.50 | 0.030 | 0.015 | 0.30 to 0.40 | 28.0 to 30.0 | ≤0.80 | 1.50 to 2.60 | 5.8 to 7.5 | – |
Hyper Duplex | S32707 | 0.03 | ≤0.50 | ≤1.50 | 0.035 | 0.010 | 0.30 to 0.50 | 26.0 to 29.0 | ≤1.00 | 4.0 to 5.0 | 5.5 to 9.5 | Co 0.50 to 2.00 |
Grade is divided by PREN, Lean(25-28), Standard(28-38), Super(38-45), Hyper(>45).
This unique composition results in physical properties that outperform many traditional stainless steels:
Property | Austenitic (304/316) | Standard Duplex (2205) | Super Duplex (2507) |
Tensile Strength (MPa) | 515-620 | 680-880 | 800-1000 |
Yield Strength (MPa) | 210-260 | 450-550 | 550-650 |
Elongation (%) | 40-60 | 25-30 | 25-30 |
Hardness (HB) | 130-180 | 250-290 | 280-320 |
Density (g/cm³) | 7.9-8.0 | 7.8 | 7.8 |
Thermal Conductivity (W/m·K) | 15-16 | 17-19 | 17-19 |
Thermal Expansion (10⁻⁶/K) | 16-18 | 13-14 | 13-14 |
PREN* range | 18-30 | 33-36 | 40-45 |
PREN (Pitting Resistance Equivalent Number)
DSS is available in various forms, with pipes, plates, and fittings being the most prevalent due to industrial demand. Seamless and welded pipes dominate oil and gas applications, while plates are common in construction and shipbuilding. Bars, flanges, valves, and forgings cater to specialized needs.
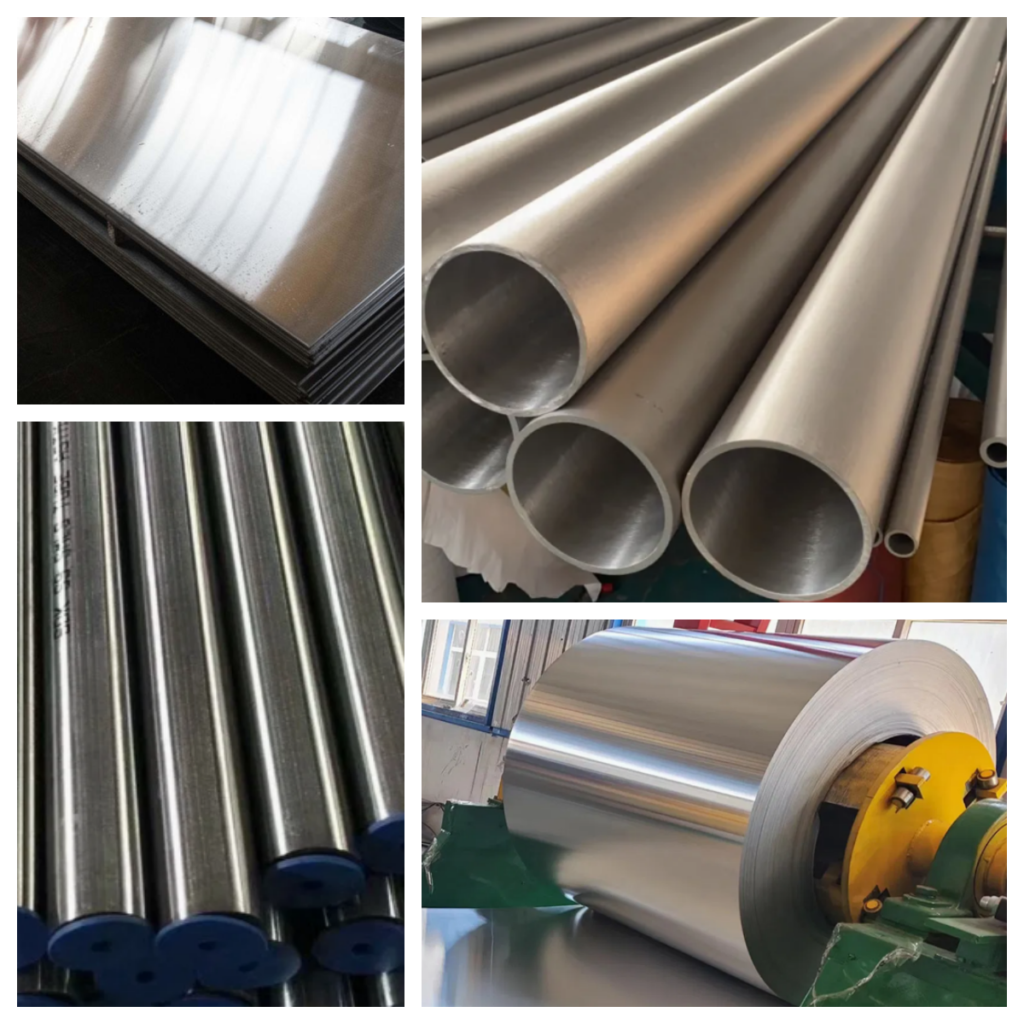
The Comparison
Duplex stainless steel provides a cost-effective solution with better mechanical strength and corrosion resistance than traditional austenitic stainless steel while being more affordable than super duplex stainless steel.
DSS vs. Traditional Stainless Steel
Compared to austenitic stainless steels (e.g., 304, 316), DSS offers double the strength, better SCC resistance, and lower nickel content, reducing cost volatility. However, it has limited high-temperature performance (above 300°C), where austenitic grades excel. Ferritic stainless steels (e.g., 430) are cheaper but lack the corrosion resistance and toughness of DSS.
Advantages Over Austenitic Steels (e.g., 304/316L):
- 2x higher strength: Reduces material thickness and weight (e.g., 40% thinner pipes for offshore rigs).
- Superior SCC resistance: Withstands chloride-rich environments (seawater, chemical plants).
- Lower lifecycle costs: Reduced maintenance and replacement frequency.
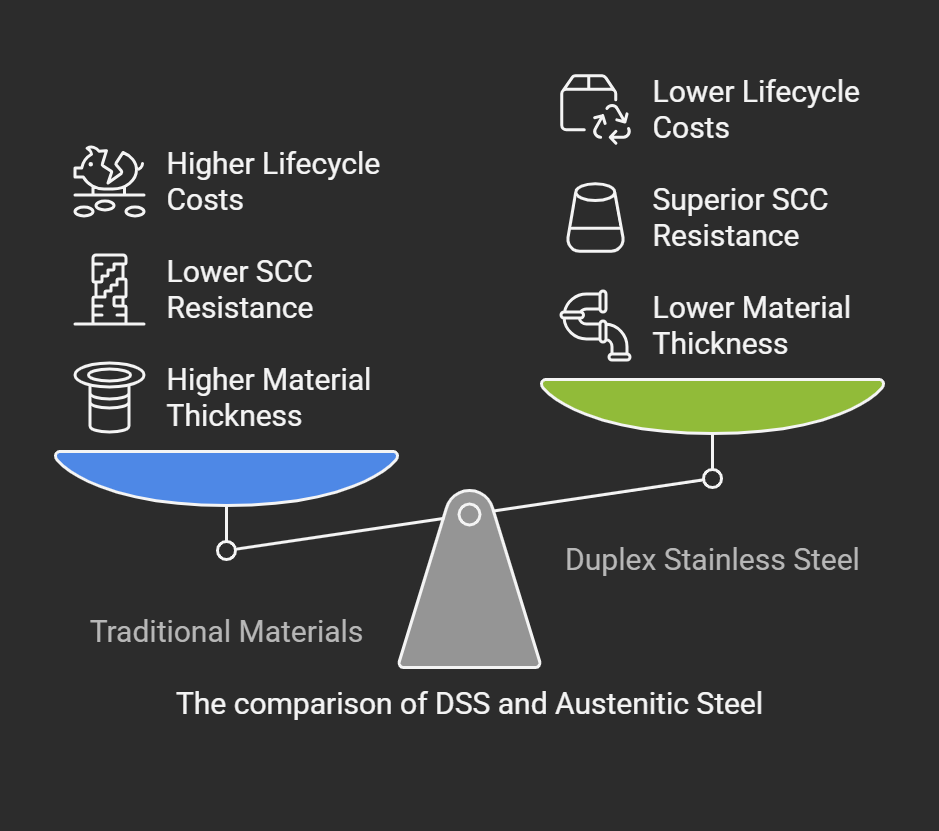
Standard duplex SS vs. Super duplex SS
The primary difference between standard duplex and super duplex grades lies in their corrosion resistance in aggressive environments. Super duplex grades contain higher levels of chromium, molybdenum, and nitrogen, resulting in PREN values above 40, compared to the 33-36 range for standard duplex grades.
In another way, standard duplex (2205) balances cost and performance, while super duplex (2507) excels in extreme conditions, with higher PREN and strength. Super duplex is more expensive due to increased Mo and Ni content, making it less common in cost-sensitive applications.
Comparative Advantages and Limitations
Property | Austenitic (304/316) | Standard Duplex (2205) | Super Duplex (2507) |
Corrosion Resistance | |||
Pitting/Crevice | Moderate | High | Very High |
Stress Corrosion Cracking | Susceptible | Resistant | Highly Resistant |
General Corrosion | Good | Excellent | Outstanding |
Mechanical Properties | |||
Strength | Moderate | High | Very High |
Toughness | Excellent | Good | Good |
Fatigue Resistance | Good | Excellent | Excellent |
Fabrication | |||
Formability | Excellent | Good | Moderate |
Weldability | Excellent | Good | Moderate |
Machinability | Good | Moderate | Challenging |
Economic Factors | |||
Material Cost | Low-Moderate | Moderate-High | High |
Weight Savings Potential | Limited | Significant | Significant |
Life Cycle Cost | Moderate | Low | Very Low |
Alloying Element Sensitivity | High (Ni) | Moderate | High |
Emerging Applications and Market Outlook
The global market for duplex stainless steel is expanding rapidly, driven by demand in oil and gas, desalination, and chemical processing. The Chinese market, in particular, is experiencing growth due to increasing infrastructure projects and advancements in local manufacturing capabilities.
According to the data from www.marketdataforecast.com, The Global Duplex Stainless Steel Market was worth USD 5.10 billion in 2024 and is anticipated to reach a valuation of USD 8.31 billion by 2032, it is predicted to register a CAGR of 6.3% during the forecast period 2024 to 2032.
Several key factors drive this growth:
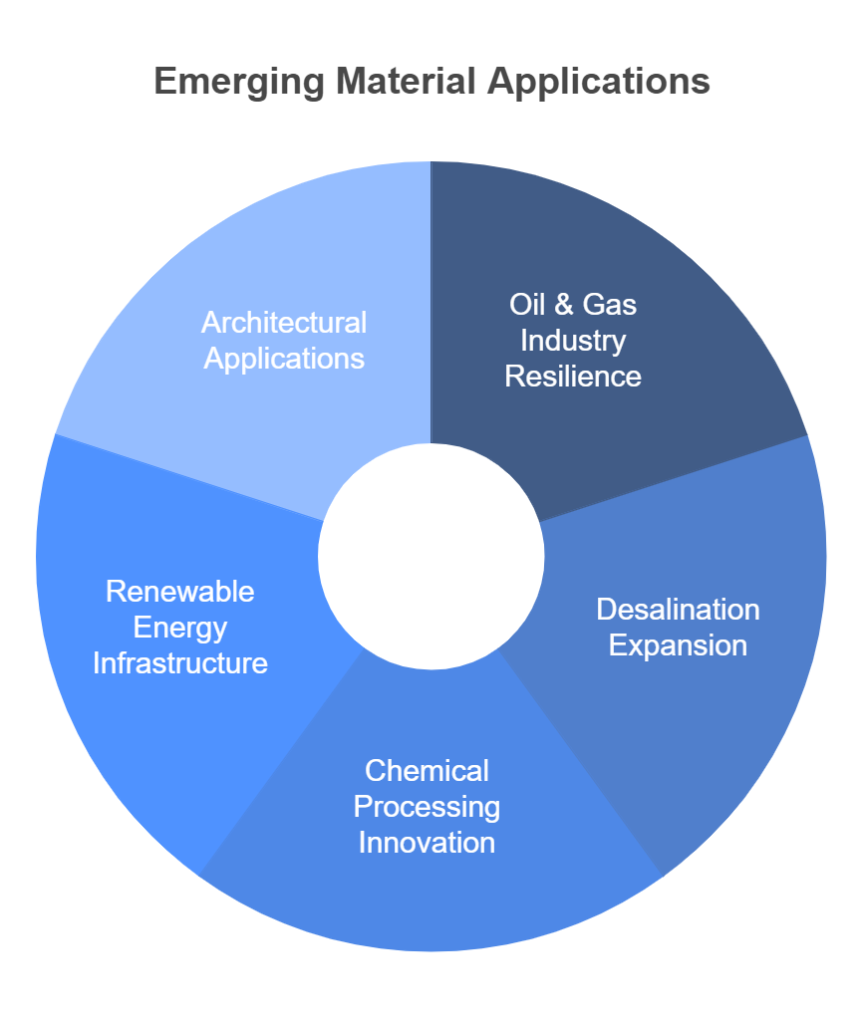
- Oil & Gas Industry Resilience: Despite fluctuations, deepwater and challenging extraction environments continue to drive demand.
- Desalination Expansion: Global freshwater scarcity has accelerated desalination projects, with duplex materials being essential for handling seawater.
- Chemical Processing Innovation: New chemical processes operating in increasingly aggressive environments require corrosion-resistant materials.
- Renewable Energy Infrastructure: Offshore wind, tidal energy, and geothermal facilities create new application areas.
- Architectural Applications: Coastal structures and buildings increasingly use duplex for structural components and facades.
China’s Competitive Advantages in Duplex Stainless Steel
Cost Advantages
China has established significant cost advantages in duplex stainless steel production through several factors:
- Integrated Production Chain: Many Chinese producers maintain integrated operations from melting to finishing.
- Scale Economies: Large production volumes spread fixed costs across more units.
- Advanced Manufacturing Technology: Significant investments in modern production facilities.
- Strategic Raw Material Access: Secured supply chains for key alloying elements.
- Workforce Efficiency: Combination of skilled labor and automation keeping production costs competitive.
This results in price advantages typically ranging from 5-15% compared to Western producers, depending on the specific product and grade.
Value-for-Money Proposition
Chinese duplex stainless steel producers have improved quality while maintaining competitive pricing, creating a compelling value proposition through:
- Quality Management Systems: Implementation of ISO 9001 and industry-specific certifications.
- International Certification: Products increasingly certified to ASTM, EN, and other global standards.
- R&D Investment: Development of proprietary production techniques and formulations.
- Customer Service Improvement: Enhanced technical support and customer service capabilities.
Supply Chain Efficiency
China’s supply chain advantages include:
- Logistics Infrastructure: Excellent port facilities and shipping connections.
- Comprehensive Product Range: Ability to source complete packages of related products.
- Flexible Production: Adaptability to varying order sizes and custom requirements.
- Digital Integration: Advanced order tracking and inventory management systems.
Popular Chinese Duplex Stainless Steel Products
Duplex Stainless Steel Pipes
- Seamless Pipes: Available in diameters from 6mm to 660mm with wall thicknesses from 0.5mm to 50mm, primarily in grades 2205 and 2507. These products have gained popularity in oil & gas, chemical processing, and power generation applications.
- Welded Pipes: Available in diameters from 15mm to 3000mm with various wall thicknesses. Chinese manufacturers have particularly strong capabilities in large-diameter welded pipes for desalination and water treatment infrastructure.
Plates, Bars, and Structural Components
- Plates and Sheets: In thicknesses from 0.4mm to 120mm, with excellent surface finish quality.
- Bars: Round, square, and hexagonal bars from 2mm to 500mm.
- Flanges and Fittings: Comprehensive range to ASME, DIN, JIS, and other standards.
Valves and Control Components
Chinese valve manufacturers have transitioned to offering complete lines of duplex stainless steel valves, particularly excelling in:
- Ball valves for severe service applications
- Control valves for chemical processing
- Gate, globe, and check valves for general industrial use
Duplex Stainless Steel Forgings
- Custom valve bodies and bonnets
- Pump components
- High-pressure vessel components
- Specialized connectors for offshore applications
Fasteners
- Bolts, nuts, and washers to international standards
- Custom fasteners for specialized applications
- Available primarily in 2205, with some 2507 availability
Heat Exchanger Components
- Tube sheets and support plates
- Shell components
- Specialized connection components
- Complete heat exchanger fabrication in duplex materials
How to Select the Most Suitable Duplex Stainless Steel Grade
When considering duplex stainless steel for an application, several key factors should guide material selection.
Environmental Factors
- Chloride Concentration: Higher chloride environments (e.g., seawater, chemical plants) favor duplex or super duplex grades.
- Operating Temperature: Duplex performs optimally between -50°C and 250°C.
- pH Level: While effective across most pH ranges, performance varies by specific environment.
- Pressure Requirements: Higher strength of duplex allows thinner walls in pressure vessels.
Economic Considerations
- Initial Material Cost: Generally higher than standard austenitic grades but lower than specialized high-nickel austenitic grades.
- Life Cycle Cost: Often significantly lower due to extended service life and reduced maintenance.
- Downgauging Potential: Higher strength allows thinner sections, offsetting some cost premium.
- Fabrication Complexity: May require more specialized welding and forming procedures. Modern DSS grades have improved weldability, but proper procedures must be followed.
Frequently Asked Questions
What is the cost-benefit analysis of choosing duplex over traditional stainless steel?
While duplex grades typically carry a 15-30% premium over standard austenitic grades like 304/316, this cost difference is often offset by several factors:
- Material Reduction: The higher strength allows thickness reductions of 30-50% in many applications.
- Extended Service Life: Depending on the application, duplex can last 2-5 times longer than austenitic alternatives.
- Reduced Maintenance: Less frequent replacement and repair intervals significantly reduce lifecycle costs.
- Operational Reliability: Fewer failures and unplanned shutdowns improve overall operational economics.
A typical calculation shows that for a seawater handling system with high chloride exposure, the total cost of ownership over 20 years can be 40-60% lower with duplex stainless steel compared to 316L, despite the higher initial investment.
Are there any limitations to using duplex stainless steel?
While offering numerous advantages, duplex stainless steels do have certain limitations:
- Temperature Restrictions: Not recommended for continuous service above 300°C or below -50°C due to microstructural changes.
- Fabrication Complexity: Requires more careful welding procedures than austenitic grades.
- Limited Formability: Less ductile than austenitic grades, limiting some forming operations.
- Intermetallic Precipitation: Susceptible to embrittlement if improperly heat-treated.
- Higher Initial Cost: Despite lifecycle benefits, upfront investment is higher.
What are the key trends in duplex stainless steel development?
- Lean Duplex Innovation: Development of lower-alloyed grades with reduced nickel content.
- Improved Weldability: New formulations with better fabrication characteristics.
- Higher Temperature Resistance: Research into grades that maintain properties at elevated temperatures.
- Specialized Surface Treatments: Enhanced surface finishes for specific applications.
- Digital Material Tracking: Integration of production data with material certifications for improved traceability.
Conclusion
Duplex stainless steels represent a material category that continues to expand its application range as industries recognize its exceptional combination of properties. The transition from traditional stainless steels to duplex grades is accelerating globally, with China playing an increasingly important role as both producer and consumer.
For industries facing corrosive environments, high mechanical loads, or demanding operational conditions, duplex stainless steel offers a compelling value proposition that extends beyond initial material costs to deliver superior lifetime performance. As global infrastructure needs grow and environmental challenges intensify, the unique properties of duplex stainless steel position it as a key material for addressing 21st-century engineering challenges.
For more information? Try these!
- Download our free guide: “Duplex Steel Selection Handbook”
- Contact our experts for a customized quotation on DSS components.