XDL
Getting your Trinity Audio player ready...
|
– Sourcing Expertise for Solar Applications
Introduction
The global solar tracking market continues to expand rapidly, with installations projected to reach over 100 GW annually by 2030. As solar tracking systems become increasingly sophisticated and deployment scales grow, the reliability and longevity of critical components, particularly bearing systems, have become paramount concerns for system operators and manufacturers.
As the solar industry rapidly expands, the need for durable, low-maintenance solar tracking systems has never been more critical. Central to these systems are plastic bearings and bushings, which must operate in harsh outdoor environments for decades with zero maintenance.
This article compares two leading materials used in these components:
- GUR® 4120/4122, a high-performance UHMWPE from Celanese
- Duracon® SW-01, a UV-stabilized POM from Polyplastics
Both materials offer distinct advantages and have proven track records in demanding industrial applications.
Specific Bearing Application Requirements
This analysis focuses on bearings designed for the following specific operational parameters, which are crucial for our audience to understand. The points raised in this article reflect these specific conditions.
- Loading Conditions: Low to medium load applications, static loads generally range from 100-800 kg per bearing assembly.
- Operational Frequency: Extremely low rotational frequency at approximately 1 rotation per 24-hour cycle (0.000012 RPM average).
- Contact Configuration: Direct metal-to-plastic contact with galvanized mild steel surfaces on both bearing faces.
- Service Life: 30-year maintenance-free operation without any lubrication, cleaning, or component replacement
- Outdoor Exposure: Continuous exposure to all weather conditions.
- Temperature Extremes: Operation through freezing conditions to summer peaks, potentially ranging from -30°C to +70°C.
- UV Resistance: Extended exposure to solar radiation demands exceptional UV stability.
- Moisture Management: Low water absorption is critical to prevent dimensional changes.
This demands materials that are not only mechanically robust but also chemically inert, dimensionally stable, and resistant to outdoor aging.
Material Overview
Ultra-High Molecular Weight Polyethylene (UHMWPE)
UHMWPE represents the pinnacle of polyethylene development, with molecular weights ranging from 3.5 to 9.2 million g/mol—approximately 10 times higher than conventional high-density polyethylene. This extreme molecular weight creates a highly entangled polymer structure that delivers exceptional mechanical properties.
GUR® 4120/4122 from Celanese
This material represents medical-grade UHMWPE that has been adapted for industrial applications. The material’s key properties are as follows:
- Extreme wear resistance
- Ultra-low friction
- High impact resistance, even below -40°C
- Very low water absorption (<0.01%)
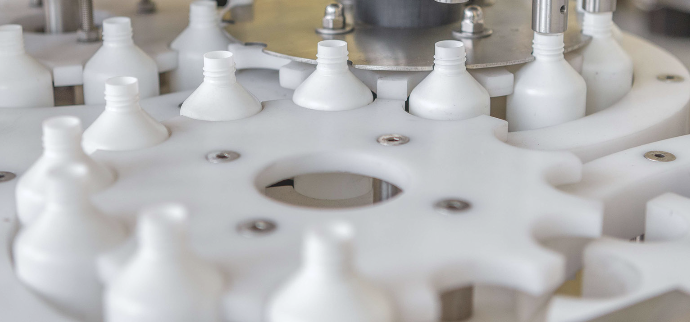
For more details, please see the following datasheet:
https://materials.celanese.com/en/products/datasheet/US/GUR%204120
Polyoxymethylene (POM)
POM is a crystalline thermoplastic engineered for precision mechanical components. The material combines high strength and stiffness with excellent dimensional stability and processing characteristics.
Duracon SW-01
This material represents a specialized formulation designed specifically for high-wear sliding applications. The POM/PE alloy structure with integrated lubricants provides enhanced performance compared to standard POM grades.
Its key properties are as follows:
- UV-stabilized for long-term outdoor exposure
- High rigidity and dimensional stability
- Good wear resistance for moderate loads
- Injection-moldable with tight tolerances (±0.05 mm possible)
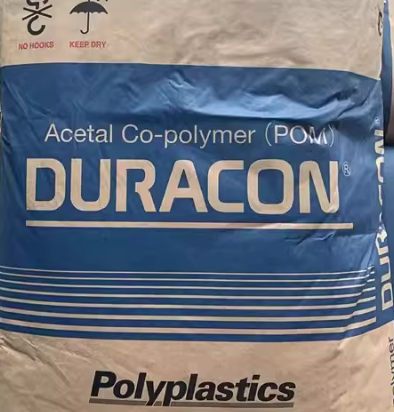
For more details, please see the following datasheet:
https://www.polyplastics.com/Gidb/GradeListSelectGradeAction.do?id=1794&_LOCALE=ENGLISH
Comparative Performance Analysis
Mechanical Properties
Property | GUR® 4120 UHMWPE | Duracon SW-01 POM | Test Method |
Tensile Strength | 39-48 MPa | 55-65 MPa | ASTM D638 |
Elongation at Break | 350-525% | 25-40% | ASTM D638 |
Flexural Modulus | 700-900 MPa | 2400-2800 MPa | ASTM D790 |
Impact Strength (Izod) | No Break | 6-8 kJ/m² | ASTM D256 |
Hardness (Shore D) | 63-67 | 78-82 | ASTM D2240 |
Wear Rate | 0.2-0.8 mm³/Nm | 0.5-1.2 mm³/Nm | DIN 53516 |
As shown on the table, UHMWPE demonstrates superior impact resistance and wear performance, while POM offers higher strength and stiffness. The exceptional elongation of UHMWPE provides better resistance to stress cracking, while POM’s higher modulus enables more precise dimensional control.
Environmental Resistance Performance
UV Stability Analysis for Long-term Exposure
• UHMWPE(GUR® 4120/4122): With the addition of suitable UV stabilizers, such as HALS (hindered amine light stabilizers) or carbon black, its outdoor durability can be significantly improved. The UV-stabilized versions can be used for direct, long-term UV exposure.
• POM(Duracon® SW-01): This is a UV-stabilized grade of POM specifically engineered for outdoor applications. SW-01 incorporates proprietary UV-resistant additives that prevent chain scission, surface cracking, and color fading caused by UV exposure.
Water Absorption Performance
The table below shows that GUR® 4120 UHMWPE’s virtually zero water absorption provides superior stability in freeze-thaw cycles, while POM’s higher absorption can lead to dimensional changes and potential ice-formation damage.
Material | 24hr Water Absorption | Equilibrium Absorption | Dimensional Change |
GUR® 4120 UHMWPE | <0.01% | <0.02% | Negligible |
Duracon SW-01 POM | 0.8-1.2% | 2.0-2.5% | 0.1-0.2% linear |
Temperature Performance for Freeze-Thaw Cycling
In freeze-thaw cycling temperature performance tests, UHMWPE(GUR® 4120/4122) generally outperforms POM(Duracon® SW-01).
Temperature Condition | GUR® 4120 Performance | Duracon SW-01 Performance |
Continuous at -30°C | Excellent flexibility, no embrittlement | Good performance, some stiffening |
Freeze-thaw cycling (-20°C to +20°C) | No degradation after 1000+ cycles | Potential for stress cracking with moisture |
Summer peak (+70°C) | Good performance, slight softening | Excellent dimensional stability |
Operational Performance Characteristics
Tribological Properties: Comparative Overview
- Self-Lubrication: GUR®(UHMWPE) provides better dry sliding due to its lower friction.
- Noise & Vibration: SW-01(POM) performs quieter in tight-fitting configurations.
- Fatigue Resistance: Both perform well under daily cyclic loads, but GUR® (UHMWPE) handles impact shock better.
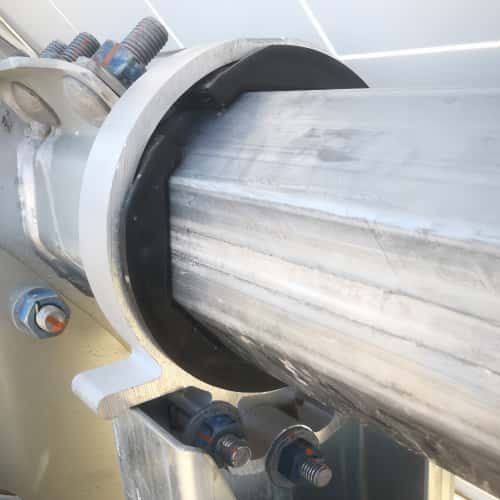
Ultra-Low Speed Operation Analysis
The extremely low rotational speed of 1 rotation per day creates unique tribological conditions that favor different material characteristics than high-speed applications.
Static vs. Dynamic Friction:
- UHMWPE: Static coefficient: 0.10-0.20, Dynamic coefficient: 0.05-0.15
- POM: Static coefficient: 0.20-0.35, Dynamic coefficient: 0.15-0.25
At ultra-low speeds, static friction dominates the bearing performance. UHMWPE’s lower static friction reduces breakaway torque and motor stress during daily positioning cycles.
Wear Analysis for 10,950 Total Cycles (over 30 years)
Both materials show minimal wear over the low-cycle lifetime, with UHMWPE providing a slight advantage in ultra-low speed conditions.
Estimated wear depth:
- UHMWPE: 0.001-0.005mm over 30 years
- POM: 0.002-0.008mm over 30 years
Real-World Application Considerations
Manufacturing and Installation
Manufacturing Characteristics
Aspect | UHMWPE | POM |
Machinability | Moderate (requires special techniques) | Excellent |
Tolerance Achievement | ±0.1-0.2mm typical | ±0.05mm achievable |
Surface Finish | 1.6-3.2 μm Ra | 0.8-1.6 μm Ra |
Tool Wear | Low | Moderate |
Moldability | Compression mold | Injection mold |
Assembly Considerations
POM’s superior dimensional precision enables tighter assembly tolerances, while UHMWPE’s flexibility accommodates slight misalignments better. Both materials can be assembled using conventional fastening methods.
Maintenance and Service Life
Expected Lifespan Analysis for 30-Year Requirement
UHMWPE (UV-Stabilized GUR® Compounds)
UHMWPE, when properly UV-stabilized, can achieve a 30+ year service life in demanding outdoor environments. The material’s molecular structure provides inherent stability, and with proper UV stabilization packages, it can withstand harsh desert conditions with high UV exposure, freeze-thaw cycling in temperate climates, and coastal humidity without significant degradation.
Field data from infrastructure applications confirms that UV-stabilized UHMWPE can maintain mechanical properties for decades under continuous outdoor exposure.
POM (Duracon® SW-01)
POM materials face more significant limitations in achieving a 30-year outdoor service life compared to UV-stabilized UHMWPE. While UV-stabilized POM grades show improved performance, the inherent sensitivity of the acetal backbone to UV radiation and moisture cycling limits long-term outdoor performance to 20 years in most climates.
The material’s dimensional stability issues with moisture absorption and its tendency toward surface degradation under prolonged UV exposure make it less suitable for applications requiring guaranteed 30-year performance without regular maintenance or replacement.
Economic Analysis (UV-Stabilized GUR® Compounds vs. Duracon® SW-01 POM)
Raw Material Cost
Even with UV additives, GUR® compounds remain 20% more cost-effective than Duracon® SW-01 on a per-kilogram basis. However, actual cost-effectiveness depends on the compound formulation quality and field performance consistency.
Processing and Manufacturing Costs
Cost Factor | UV-Stabilized GUR® Compounds | Duracon® SW-01 (POM) |
Processing Method | Compression molding or CNC | Injection molding |
Tooling Cost | Low (simple molds or direct machining) | Medium to high (complex tooling) |
Production Cycle Time | Longer (batch molding) | Faster (automated, scalable) |
Scrap/Rework Risk | Moderate (warping, shrinkage) | Low (excellent mold behavior) |
Generally speaking, for large, low-complexity parts, GUR® is more economical. For small, high-precision parts, SW-01 is more efficient due to better dimensional repeatability.
Durability and Total Cost of Ownership (TCO)
Metric | UV-Stabilized GUR® Compounds | Duracon® SW-01 (POM) |
Wear Resistance | ★★★★★ | ★★★★☆ |
UV Stability | ★★★★☆ (depends on additive loading) | ★★★★★ (formulated and validated) |
Dimensional Stability | ★★☆☆☆ (thermal expansion) | ★★★★★ (very stable) |
Water & Chemical Resistance | ★★★★★ | ★★★★☆ |
Field Lifespan (30+ years) | Achievable with proven formulation | Achievable, proven in UV-heavy sites |
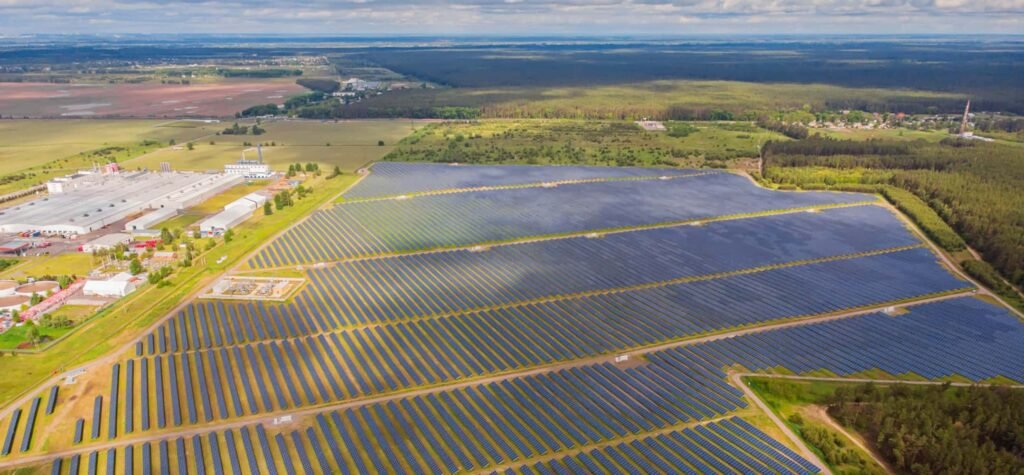
Application Recommendations for Specific Requirements
Primary Material Recommendation: GUR® 4120/4122 UHMWPE
Based on the comprehensive analysis of the specific bearing requirements, UHMWPE emerges as the clear preferred choice for this application. The decision is driven by several critical factors:
- 30-Year UV Resistance: UHMWPE with UV stabilizers ensures reliable performance throughout the entire service life without degradation of mechanical properties.
- Minimal Water Absorption: With <0.02% water uptake, UHMWPE eliminates dimensional changes and freeze-damage risks that could compromise bearing function.
- Freeze-Thaw Durability: Excellent performance through thousands of freeze-thaw cycles without cracking or property degradation.
- Ultra-Low Speed Performance: Superior breakaway torque characteristics reduce motor stress during daily positioning cycles.
- Maintenance-Free Operation: Self-lubricating properties ensure consistent performance for 30 years without any intervention.
Why POM is Not Recommended for This Application
Despite POM’s excellent general properties, several factors make it unsuitable for the specific 30-year maintenance-free requirement:
- Water Absorption: 2-2.5% equilibrium moisture absorption creates dimensional instability and freeze-thaw vulnerability
- Long-Term Durability: Insufficient field data to confirm 30-year maintenance-free operation in harsh outdoor conditions
Conclusion
For the specific bearing application requiring 30-year maintenance-free operation with low-medium loads, 1 rotation per day, galvanized steel contact, and full outdoor exposure including freeze-thaw conditions, GUR® 4120/4122 UHMWPE is the definitive choice between the two given materials.
Technical Appendix
Material Specifications Summary
GUR® 4120 UHMWPE
- ASTM D4020 classification: Type 1, Class 1, Grade 1
- FDA compliance: 21 CFR 177.1520
- Operating temperature range: -200°C to +80°C continuous
- Radiation resistance: Excellent (suitable for sterilization)
Duracon SW-01 POM
- ISO 9988-1 classification: POM-C
- UL 94 flame rating: HB
- Operating temperature range: -40°C to +100°C continuous
- Chemical resistance: Excellent to most chemicals
Industry Standards and Certifications
- ASTM D6778: Standard Test Methods for Compressive Properties of Plastic Lumber
- ISO 527: Determination of tensile properties
- ASTM G154: UV exposure testing
- IEC 61215: Solar panel qualification standards
Contact Information
For technical consultation on material selection for your specific solar tracking application, please contact our engineering team.
Our experts can provide detailed analysis, material samples, and application-specific recommendations to ensure optimal bearing performance for your installation requirements.
This analysis is based on published material specifications, industry testing standards, and field experience data. Specific applications should be validated through appropriate testing and consultation with material suppliers.